- Home »
- Passion For Quality »
- Flat, Bright & Dry
Flat, Bright & Dry
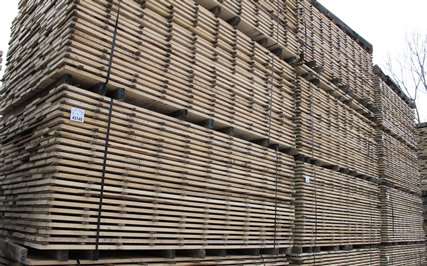
We set the standard for some of the best drying practices in the industry. It takes time and extra effort, but we believe that it is worth it. Below are a few of the ways that we express our commitment to product quality:
Flat
We are passionate about producing the flattest, most useable product for our customers. Once the lumber is placed on stickers at our automatic stacking machine center, the bundle is tightly securely using two nylon bands to maintain absolute uniformity of each bundle during transport to and from the kilns. We also ensure that each piece of lumber receives the maximum level of support and stability possible while drying.
Stickers are uniformly placed under every layer of lumber in 12" increments. Between each bundle, narrow bolsters are placed directly under each sticker, and weighted concrete roofs are placed over every stack to provide maximum stabilization to the top layers of lumber. Stacks of lumber also receive a 2” thick bottom course, providing a solid foundation and preventing the bottom layers of lumber from waffling.
Bright
We take care to preserve the brightness of our lumber throughout every stage of our processes. Shortly after being placed on stickers, all white woods are quickly loaded into kilns to mitigate the possibility of stain or darkening of the sap wood. The brightness of Red & White Oak lumber is also carefully preserved during air drying through the use of our our fully automated dipping station where the lumber is dipped in a anti-stain / brightening solution. Narrow bolsters and Breeze Dried™ fluted stickers are used to eliminate shadow or stain during drying. Low temperature kiln schedules are also used to maintain the absolute brightest appearance of the wood, both inside and out.
Dry
An automated sawdust fired boiler system is utilized on site to generate all the heat needed to operate our 220,000 BF of dry kilns. State-of-the-art computerized controllers are used to carefully monitor and adjust each kiln, and experienced operators monitor kiln performance continuously. Once the lumber has been properly dried and stress relieved, lumber is stored indoors in our modern 31,500 SF warehouse.